Every year across the USA, HVAC technicians face far more workplace risks than most realize: maintenance and repair jobs alone were linked to nearly 475 fatal injuries in 2021, representing almost 10% of all installation, maintenance, and repair fatalities that year (Source). Behind those numbers lie severely underreported non‑fatal incidents—sprains, fractures, electrical shocks—that could all be traced back to missing risk assessments, faulty PPE, or unsafe refrigerant handling.
And the stakes are getting higher. The EPA now imposes daily fines of up to $69,733 for refrigerant-related violations—and $57,617 for repeat offenses (Source). Meanwhile, OSHA is tightening oversight as workplace incidents in the HVAC trade continue above national averages .
In this blog, we’ll drill down into essential areas every HVAC field service business in the U.S. must master: compliance with EPA and OSHA, robust safety protocols, proper refrigerant management, mandatory training, and maintaining indoor air quality and energy efficiency. Because cutting corners isn’t just a regulatory risk—it’s a threat to your team, your reputation, and your bottom line.
Why Compliance and Safety Standards Matter in HVAC Field Services
Compliance is more than paperwork—it’s a legal mandate with real-world consequences. In 2023, OSHA reported 5,283 fatal work injuries across U.S. industries (3.5 per 100,000 workers), and installation, maintenance, and repair classified roles carry a particularly high risk—about 8.8 fatalities per 100,000 workers (Source). For HVAC field service businesses, a single violation—such as bypassing risk assessment or ignoring electrical safety protocols—can lead to OSHA penalties averaging $13,653, with maximum fines much higher for serious or repeated offenses (Source).
Beyond legal consequences, compliance drives customer trust. Clients perceive safety-conscious HVAC providers as professional and dependable—crucial for reputation and repeat business. Conversely, safety incidents can damage credibility and incur escalated insurance premiums.
From an operational perspective, non-compliance can cause unplanned downtime, worker compensation claims, and costly insurance audits. Industry data shows HVAC firms typically log over 37,000 injury and illness claims annually, with nearly all tied to safety or health code violations . That level of exposure not only hurts efficiency but also inflates insurance costs and disrupts scheduling.
In a competitive market, maintaining adherence through regular audits, rigorous risk assessments, and mandatory training isn’t optional—it’s essential. It safeguards your workforce, reassures clients, and strengthens your brand while keeping regulatory fines and operational risks at bay.
Key U.S. Regulatory Bodies & Standards to Know
Navigating the complex web of regulations is essential for HVAC field service businesses aiming to stay compliant, safe, and efficient.
OSHA: Worker Safety & PPE Standards
OSHA oversees workplace safety through regulations like 29 CFR 1910.132, which mandates hazard-driven risk assessments and employer-provided PPE (eye, face, respiratory, electrical protection). In FY 2024, OSHA conducted approximately 34,700 federal inspections, with “Eye and Face Protection” and “Electrical Protective Equipment” frequently cited standards (Source). Meeting these requirements not only reduces incidents and injuries—it helps avoid citations and fines.
EPA: Section 608 & HFC Phasedown
Under Section 608 of the Clean Air Act, technicians must be EPA-certified to handle refrigerants—Types I, II, III, or Universal. The regulation enforces strict practices: no venting, mandatory refrigerant leak tracking, prompt repairs, and detailed documentation lasting at least three years (Source). With the ongoing HFC phasedown, staying certified and compliant saves your company from substantial EPA penalties.
DOE & Energy Efficiency Regulations
DOE regulations leverage standards like ANSI/ASHRAE 90.1 to enforce minimum energy-performance levels for commercial HVAC systems. Since its 2016 adoption, the standard has delivered up to a 8% reduction in energy use—helping both the environment and clients’ energy bills.
ASHRAE: Indoor Air Quality & System Design
ASHRAE 62.1/90.1 standards guide HVAC system layouts and indoor air quality (IAQ), with proper ventilation proven to reduce workplace IAQ symptoms ranging from headaches to respiratory irritation (Source).
National Occupational Standards
While not federally mandated, these benchmarks outline core competencies for technicians—from electrical safety to refrigerant handling, enhancing proficiency and easing OSHA/EPA audit preparation.
State-Level Codes
States often implement stricter standards. For instance, California Title 24 Part 6 mirrors and even exceeds ASHRAE 90.1 for energy efficiency—make sure your field teams are up to date on any such statewide regulations.
Refrigerant Management & the HFC Phasedown
Proper refrigerant management is central to HVAC compliance in the U.S.—especially under EPA’s Section 608 and the HFC phasedown.
Overview of Section 608 & Refrigerant Handling
Under Clean Air Act Section 608, technicians must be EPA-certified to handle refrigerants and follow strict protocols: no venting, mandatory leak testing, recovery, reuse, and detailed record-keeping for three years. Any release during service is prohibited, enforcing safer handling in the field.
Licensing & Documentation
Section 608 certification comes in four types (I, II, III, Universal) depending on equipment handled. Certified technicians must keep certification onsite, log refrigerant type, recovery dates, quantities, and where transfers occurred—ensuring full compliance and accountability.
Alternatives to HFCs
With the EPA rolling out the HFC phasedown under the AIM Act aiming to cut HFC use by 85% by 2036, the industry is rapidly adopting low‑GWP options:
- Natural refrigerants: CO₂, ammonia, propane—all with near-zero global warming potential.
- Next-gen synthetics: HFOs, with only ~0.1% GWP of traditional HFCs—though they require careful handling due to environmental breakdown products.
Environmental Impact
HFCs, while ozone-safe, are potent greenhouse gases—R‑410A is approximately 2,088 times more climate-damaging than CO₂ (Source). Left unchecked, HFC emissions could grow from 0 to 1.2 Gt CO₂e by 2010, underscoring the urgent need for phasedown epa.gov+1epa.gov+1. The AIM Act, aligned with the Kigali Amendment, mandates steep phasedown through 2036.
Risk Assessment and Safety Protocols in the Field
HVAC field work brings a wide range of hazards — from electrical shocks and chemical exposures to ergonomic injuries and falls. Recognizing and managing these risks through routine risk assessments and strict safety protocols is essential to compliance and the protection of your crew.
Common HVAC Hazards
- Electrical Risks: Faulty wiring, live circuits, and arc-flash risks are leading causes of injury. OSHA data shows that contact with electricity causes approximately 37% of non‑fatal electrical injuries in construction roles (Source).
- Chemical/Refrigerant Exposure: Refrigerants and cleaning solvents can cause burns or respiratory harm without proper PPE and training .
- Ergonomic Strain: HVAC techs handle heavy units, repetitive lifting, and awkward positions—leading to musculoskeletal disorders, which OSHA identifies as the top source of workers’ comp claims (Source).
Importance of Routine Risk Assessment
According to recent industry guidance, structured risk assessments reduce incidents and improve compliance . A typical assessment should:
- Identify hazards (electrical, chemical, ergonomic).
- Evaluate risk likelihood and severity.
- Apply controls (engineering, admin, PPE).
- Document findings and revisit annually or after major site changes.
Essential Safety Protocols
- Lockout-tagout & Electrical Safety: Always de-energize systems before work, use insulated tools, verify grounding, and follow NFPA/OSHA electrical work practices.
- PPE Usage: Ensure hard hats, goggles, insulated gloves, respirators, and steel-toed boots are worn per hazard type.
- Ergonomic Best Practices: Adopt mechanical lifts, team-lift heavy units, and rotate tasks to prevent strain.
- Chemical Handling Training: Technicians should know refrigerant hazards, SDS protocols, and recovery/recycling procedures to maintain safety and compliance.
Importance of Personal Protective Equipment (PPE)
Ensuring effective Personal Protective Equipment (PPE) is not just best practice—it’s a legal requirement under OSHA’s General Duty Clause and specific standards like 29 CFR 1910.132 & .133 – .138, which mandate employers to provide PPE at no cost, based on documented hazard assessments such as for electrical work and chemical exposure.
HVAC-Specific PPE Essentials
HVAC technicians face diverse hazards including refrigerant leaks, arc-flash risk, and exposure to fumes. Technicians should be equipped with:
- Insulated gloves and arc-rated flame-resistant clothing for electrical safety
- Safety goggles or full-face shields to guard against chemical splashes and airborne debris
- Respirators (half- or full-face, NIOSH-approved) for protection during refrigerant handling and solvent use.
- Hard hats, steel-toe boots, and hearing protection in line with OSHA & ANSI standards
Employer Responsibilities
By law, HVAC employers must:
- Conduct thorough site-specific hazard assessments
- Provide proper-fitting PPE suited to identified risks
- Train employees on proper PPE use, maintenance, and disposal
- Replace worn or damaged PPE immediately.
Failure to comply can lead to citations—with lack of employer-paid PPE being a frequent violation—and increase the risk of incidents like chemical burns or electrical trauma.
Mandatory & Ongoing Training Requirements
For HVAC field service businesses, continuous training isn’t optional—it’s a critical component of safety, compliance, and workforce excellence.
Licensing Requirements (EPA Section 608)
To legally handle refrigerants in the U.S., technicians must obtain EPA Section 608 certification (Type I, II, III, or Universal) by passing a proctored exam covering refrigerant handling and safety practices. The EPA’s expanded regulations now include HFC-based refrigerants, and the use of certified recovery equipment is mandatory—noncompliance risks fines and certification loss.
Importance of Refresher Courses
Ongoing refresher training keeps technicians up to date with evolving standards—like recent leak-monitoring requirements—and reinforces safe service habits. OSHA emphasizes continuous education on hazard recognition and PPE use, reducing accidents and ensuring regulatory compliance .
Training Reduces Workplace Accidents
A synthesis by CDC/NIOSH found that targeted safety training—including first aid—significantly lowers workplace injuries. Likewise, broader OSHA findings show that employer-led inspections and training can reduce injury rates by up to 9%, with a 26% drop in related costs. In the HVAC context, regular, interactive training helps teams internalize proper refrigerant handling, electrical safety, and risk assessment—preventing slips, chemical exposure, and ergonomic strain.
Alignment with National Occupational Standards
Embedding National Occupational Standards into training ensures technicians attain verified competency in core tasks—from electrical safety to refrigerant management—boosting audit readiness and overall performance.
By formalizing initial certifications and layering ongoing refresher training aligned with national benchmarks, HVAC field service businesses in the U.S. significantly enhance safety, compliance, technician proficiency, and cost-effectiveness.
Indoor Air Quality & Energy Efficiency Compliance
Indoor air quality (IAQ) and energy efficiency aren’t just performance metrics—they’re vital to occupant health, system longevity, and regulatory compliance.
How IAQ Impacts System Performance & Health
ASHRAE estimates that integrating better ventilation, filtration, and controlling dampness can reap up to $20 billion in annual economic benefits—from reduced sick days to improved productivity. Proper IAQ management also extends HVAC equipment life by 20–50% and cuts energy use by up to 20% (Source). Moreover, predictable IAQ practices lower risks of respiratory illnesses and “sick building syndrome” symptoms.
ASHRAE Standards for IAQ
ASHRAE Standards 62.1 and 62.2 set minimum ventilation rates (e.g., 8.3 L/s per person), with higher recommendations delivering measurable performance gains and reduced symptoms. Following these standards during installation and maintenance helps HVAC teams comply with both OSHA and building code requirements—while ensuring healthier environments.
DOE’s Energy Compliance Measures
Since January 2023, DOE standards mandate minimum SEER, SEER2, and HSPF ratings for residential HVAC equipment—SEER14 in the North and SEER15 in the South—delivering between $2.5 billion to $12.2 billion in energy bill savings over 30 years. The move toward performance-based codes (e.g., IECC and ASHRAE 90.1) now targets 7–58% HVAC energy savings depending on system configuration.
Why Field Techs Must Stay Updated
Keeping pace ensures proper compliance during audits, and helps diagnose inefficiencies emerging from outdated installations. Technicians trained in IAQ standards and current energy codes can enhance client satisfaction by offering greener, healthier, and code-compliant solutions—positioning your business as a trusted industry leader.
Regular Audits & Documentation Best Practices
Regular audits—whether internal or external—and meticulous documentation are essential for maintaining compliance, ensuring safety, and managing refrigerants effectively.
Internal vs External Audits
- Internal Audits are self-assessments done by your team or a third party. They’re proactive tools to catch gaps before regulators arrive. Industry best practices outline a 4-stage audit process: preparation, gap analysis, remediation, and review.
- External Audits are conducted by regulators or accredited auditors. They validate compliance with federal regulations (OSHA/EPA) and industry standards, and a thorough internal audit significantly improves readiness .
What to Track
- Safety Checks: Keep records of electrical inspections, PPE assessments, risk assessments, and corrective actions taken.
- Refrigerant Logs: Under EPA Section 608, for systems containing ≥50 lbs, maintain detailed logs of refrigerant recovered, added, and leak inspections, and file leak reports if lost >125% of full charge. Track disposal and recovery dates, types, and amounts monthly (Source).
- Maintenance History: Document all service dates, parts replaced, energy performance reports, and IAQ checks. Include SEER/HSPF ratings for residential units to show DOE compliance.
Compliance Reporting Tools
Leverage digital solutions—like refrigerant tracking platforms, CMMS, or compliance software—to automate logging, send leak alerts, and store technician certifications. These systems can reduce refrigerant leaks by up to 45% and help avoid fines of $37,500/day under EPA rules;
By implementing a structured approach to audits, tracking all critical safety and refrigerant metrics, and using robust reporting tools, HVAC field service businesses not only maintain regulatory compliance but also foster safer operations, reduce risks, and ensure reliable service delivery.
In the fast-evolving U.S. HVAC landscape, safety and compliance are not just regulatory obligations—they are operational imperatives that safeguard your team, protect clients, and uphold your company’s reputation. From OSHA’s safety protocols to EPA’s refrigerant rules and ASHRAE’s indoor air quality benchmarks, the HVAC industry demands proactive responsibility at every level of service.
Being reactive is no longer enough. Fines for non-compliance can reach up to $37,500 per day, while neglecting basic risk assessment or training can lead to serious injuries, loss of customer trust, and operational downtime. Adopting a structured, proactive compliance strategy—grounded in continuous training, robust documentation, and regular audits—positions your business as a leader in safe, efficient, and sustainable field service.
See how FieldAx can transform your Field Operations.
Try it today! Book Demo
You are one click away from your customized FieldAx Demo!
Author Bio
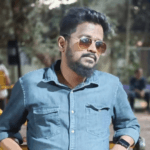
Palani Kumar
Palani Kumar is a seasoned digital marketing professional with over 13 years of experience in crafting impactful strategies for B2B brands.
As the marketing lead at FieldAx, he focuses on bridging the gap between technology and business growth, simplifying complex field service management concepts into valuable insights.
Passionate about delivering informative and practical content, Palani writes about industry trends, best practices, and innovations that help businesses optimize their field operations.
When not working on marketing strategies, he enjoys exploring history, engaging in thought-provoking discussions, and appreciating the balance between technology and tradition.