Wearable
Inventory tracking in the field refers to managing and monitoring inventory assets used outside centralized locations by mobile teams or field technicians. This ensures accurate, real-time visibility of tools, parts, and equipment across multiple locations. It is common in utilities, construction, telecommunications, oil and gas, and field service management.
- Reduce downtime and inventory shortages
- Improve service delivery timelines
- Minimize asset losses
- Enable real-time updates and seamless field-to-hub communication
Common Types of Field Inventory Items
- Spare parts (fuses, filters, valves)
- Specialized tools and instruments
- PPE and safety kits
- Testing and diagnostic devices

Functionality
- Inventory Tracking Systems: Digital platforms to monitor stock levels, usage history, and automate alerts.
- Mobile Inventory Tracking Apps: Enable technicians to log consumption, check stock, and request supplies in real time.
- Asset Tracking Software: For high-value tools, integrated with barcodes, QR codes, or RFID.
- Cloud-Based Integration: Synchronizes data for real-time visibility and reduces manual errors.
- GPS and RFID Tagging: For location-based monitoring and asset identification.
Functionality of Mobile Inventory Tracking
- Real-time stock visibility at job sites and in vehicles
- Barcode/RFID scanning for verification
- Consumption logging and automatic updates
- Replenishment ordering directly from the field
Common Issues & Failure Patterns
- Data Inaccuracy: Manual errors or delayed updates cause mismatches.
- Equipment Misplacement: Improper logging results in lost or idle tools.
- Tag Damage: RFID/barcode tags fail in harsh environments.
- Sync Failures: Poor connectivity prevents timely updates.
Preventive & Corrective Measures
- Periodic audits (weekly/monthly)
- Use rugged devices and durable tags
- Implement smart tags and automation
- Offline-capable tracking apps with sync-on-connect feature
- Train technicians on accurate logging protocols
Integration with Broader Systems
- ERP Systems: Aligns inventory with procurement and finance.
- FSM Platforms: Connects job scheduling and parts availability.
- Asset Management Systems: Tracks lifecycle and maintenance history.
Applications Across Industries
- Telecom: Managing spares for installations and repairs
- Utilities: Tracking transformers, fuses, and critical assets
- Construction: Ensuring on-site tool availability
- Healthcare: Managing mobile diagnostic kits and PPE
- Oil & Gas: Monitoring offshore or remote site equipment
Challenges in Implementation
- High upfront costs for systems and hardware
- Connectivity limitations in remote sites
- Technician resistance to digital adoption
- Data security and privacy compliance
Our trusted customers
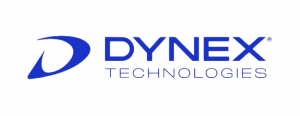
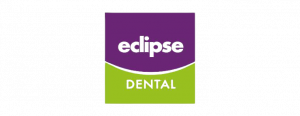
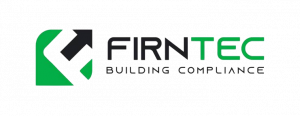
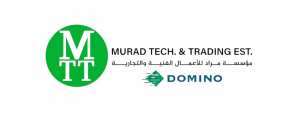
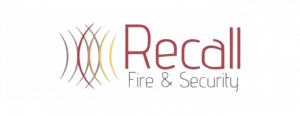
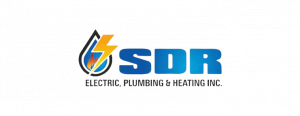
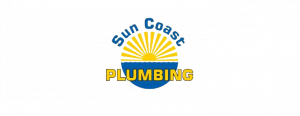
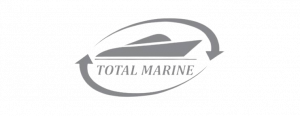
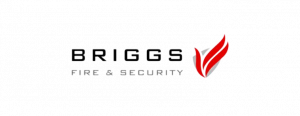
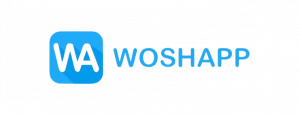