What is Torque?
Torque is the rotational force that causes an object to turn around an axis. When you tighten a screw or bolt, you’re applying torque. It’s measured in units such as Newton-meters (Nm) or inch-pounds (in-lb), depending on regional standards.
In manufacturing, torque is not just about tightening — it’s about controlling how much force is applied so that parts are secure, but not damaged.
What is Torque Specification?
Torque Specification is the defined amount of torque that must be applied to a fastener, like a screw or bolt, during assembly. This value is calculated and approved by engineers and documented in technical drawings or work instructions.
The goal is to ensure components are fastened:
- Firmly enough to hold during operation,
- But not so tight that they cause damage or stress.
Importance in Medical Device Manufacturing
Medical devices often have small, delicate components that need precise assembly. Applying incorrect torque can lead to serious issues such as:
- Cracked plastic casings
- Damaged threads in metal parts
- Faulty sealing in electronic enclosures
- Risk of failure during patient use
Torque specification ensures:
- Safety for patients and users
- Compliance with regulatory standards (such as ISO 13485, FDA regulations)
- Consistency across production batches
- Reliability in performance of the device
Where Torque Specifications Are Used
Torque specifications are found across multiple assembly points in a medical device production line, such as:
- Mechanical fastening: To assemble frames, supports, or metal parts
- Electronics integration: Mounting PCBs and fixing sensors
- Sealed housings: Ensuring proper torque for water or dust-resistant device covers
- Implant-related tools: Where torque directly affects surgical outcomes
Tools Used for Applying Torque
Specialized tools are required to apply the right torque accurately:
- Torque wrenches: Used for larger mechanical assemblies
- Torque screwdrivers: Suitable for fine and delicate work
- Digital torque tools: Provide real-time torque feedback and improved control
- Automated systems: Used in high-volume environments for speed and consistency
All torque tools must be routinely checked and calibrated to maintain accuracy.
Implementation in Manufacturing & Installation
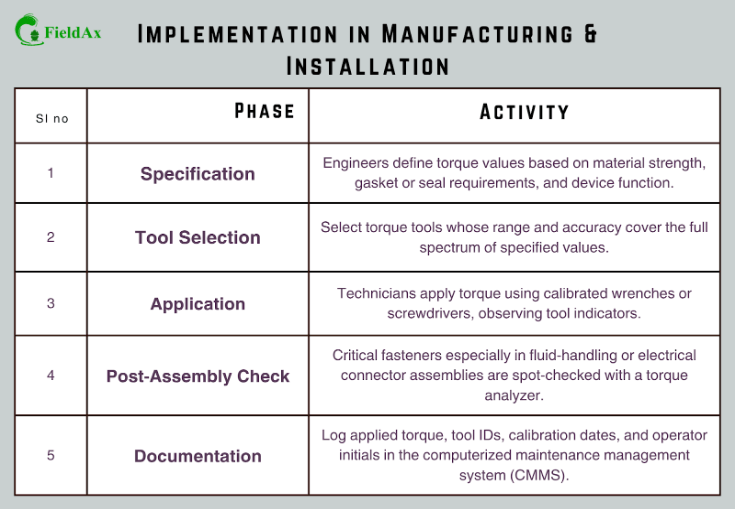
Common Problems in Torque Application
Even with defined specifications and proper tools, some challenges commonly arise:
Over-Tightening
This happens when more torque is applied than necessary. It can strip threads, crack materials (especially plastics), or deform the fastener. This typically occurs due to manual over-torquing or using the wrong tool.
Under-Tightening
Too little torque can cause screws or bolts to loosen over time, especially in vibrating environments. This may lead to malfunction, rattling, or leakage — depending on the part.
Tool Miscalibration
Torque tools that haven’t been calibrated in a while might show incorrect readings, which leads to consistent errors in torque application without the operator even realizing it.
Incorrect Tool Selection
Using a tool outside its recommended torque range or using mismatched bit sizes may result in poor torque control, slippage, or damage.
Improper Torque Sequence
In cases where multiple fasteners need to be tightened (like on a sealed housing), tightening them in the wrong order may lead to uneven pressure, warping, or broken seals.
Environmental Influences
Temperature and humidity can affect both materials and tool performance. For example, expansion or contraction of plastics can impact the clamping force.
Missing or Unclear Documentation
Sometimes, the torque value is not listed or is ambiguous. This leads to uncertainty and increases the chance of improper tightening.
Human Error or Fatigue
In manual assembly settings, repetitive tasks can cause operators to lose consistency — especially when relying on feel instead of proper tools.
How These Problems Are Usually Addressed
To prevent over-tightening, torque-limiting tools are used. These tools are either set to stop or “click” once the specified torque is reached, ensuring that no extra force is applied beyond the limit. Similarly, under-tightening is resolved by training operators to always follow the torque values indicated in work instructions and by using tools that show or confirm the applied force.
Tool miscalibration is addressed through a regular calibration schedule. Each torque tool is tested against a standard, and if it’s off, it is recalibrated or taken out of service until fixed. It’s common practice to label tools with their last and next calibration date to avoid misuse.
When the wrong tool is selected, it’s often due to unclear guidance or lack of familiarity. Tool selection charts or color-coded systems help workers match the right tool to the right job. Training sessions are also used to explain which tools work within specific torque ranges.
Improper torque sequence is typically avoided by including a torque order diagram in the work instructions. In assemblies like sealed covers, following a defined sequence ensures even distribution of force. The use of visual markers or numbering can also help operators keep track.
Environmental issues are managed by maintaining a controlled workspace, especially in cleanrooms or climate-controlled zones. In some cases, special materials or torque adjustments are made based on conditions like high humidity.
If torque values are missing from documentation, the standard procedure is to stop the process and escalate the issue to a supervisor or quality engineer. No part should be assembled based on guesswork. Once clarified, the documentation is usually updated to prevent future confusion.
Finally, to minimize human error and fatigue, many production lines incorporate semi-automated torque drivers or rotate workers between tasks. Real-time torque monitoring tools may also be used to provide immediate feedback to the operator.
Torque Specification is a fundamental part of medical device manufacturing. It ensures that every connection in a device is secure, consistent, and safe. For newcomers, learning about torque isn’t just a technical skill — it’s a way to contribute to the overall quality and reliability of life-saving products. Every screw, every tool, and every measurement has a purpose — and torque is one of the most important forces behind that precision.
Our trusted customers
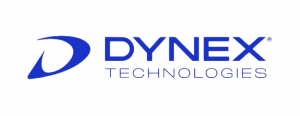
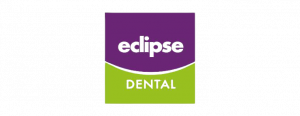
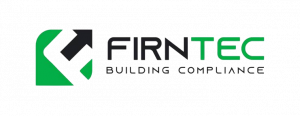
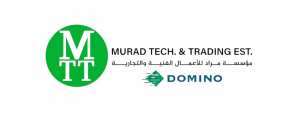
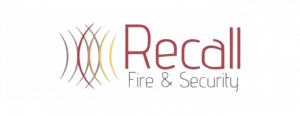
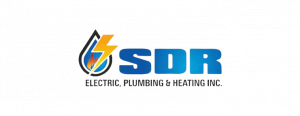
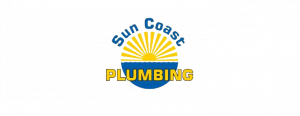
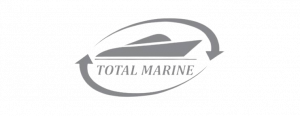
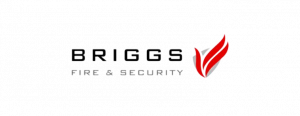
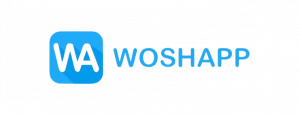